What's more, although China has been able to independently produce aviation aluminum-clad alloys, there is still a certain gap with the aviation aluminum-clad alloys produced in the United States and other countries in damage tolerance performance, maximum allowable deformation, as well as the ductility of plates and other key properties. Some key materials and core parts of the space shuttle are still not self-sufficient. To solve the problem of aluminum alloy
The "bottleneck" problem of materials still needs to improve China's independent innovation ability, establish a mechanism of complementary advantages and close cooperation between upstream and downstream of the industrial chain, shorten the production cycle, form a sustainable innovation ability, and realize the strategic transformation from a large material country to a powerful material country.
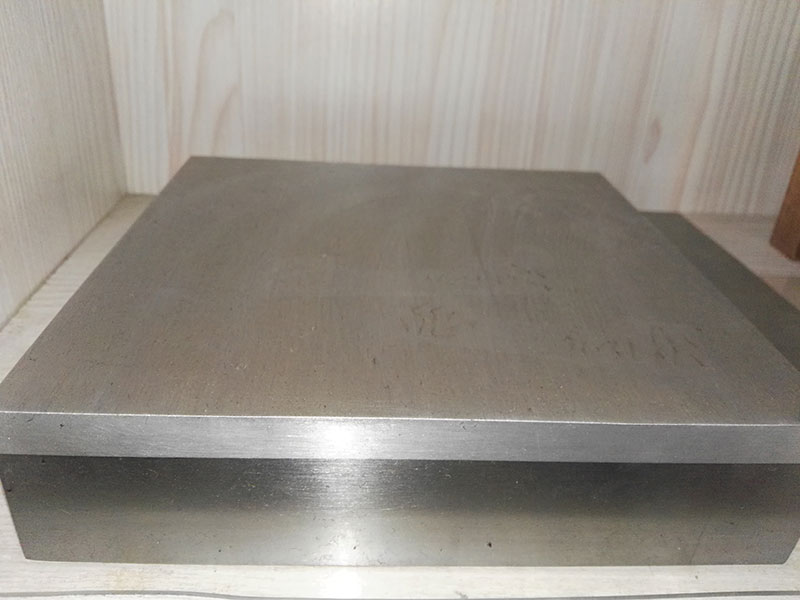
Clad aluminum refers to wrapping high-purity aluminum on the outer surface of duralumin alloy. As aluminum is an active metal, the part in contact with air will form a layer of dense alumina film, thus providing good corrosion protection for duralumin alloy. Because pure aluminum is softer and duralumin alloy has higher hardness, the physical and chemical properties of the two are quite different, so they are directly rolled on the surface of duralumin alloy
Coating pure aluminum will lead to defects such as uneven aluminum coating and fracture of aluminum coating, so there are certain requirements for aluminum coating process of duralumin alloy. Duralumin alloy has good mechanical properties and corrosion resistance after aluminizing process, annealing, solution heat treatment and deformation treatment.
Aircraft is a complex system. In the design process, each component needs to select specific materials according to its functions. The aircraft surface material is also called skin material. Because it is in direct contact with the atmosphere, it has more stringent requirements on material performance. With the rapid development of aerospace technology in recent years, the flight speed of aircraft is getting faster and faster. The supersonic flight speed has reached 2.2 MA (Mach) per hour
In fact, the local area of the fuselage is at a high temperature above 150 ℃ for a long time during flight, which puts forward higher requirements for the high-temperature service performance of aircraft skin materials. 7xxx series aluminum alloys have excellent mechanical properties at room temperature, but their properties decay seriously with the increase of temperature, which can not meet the needs of aircraft surface skin materials. 2024 aluminum alloy has less mechanical properties than 7050 aluminum alloy at room temperature,
However, its high-temperature service performance is good. It is pointed out that when the working temperature exceeds 150 ℃, the mechanical properties of 2024 aluminum alloy will exceed 7050 aluminum alloy, so it is often used as aircraft skin material.
During flight, the aircraft skin materials are in direct contact with the high-altitude atmosphere, which is easy to be corroded. Therefore, the corrosion resistance should be fully considered while meeting the high-temperature service performance. The main additive element of 2024 aluminum alloy is Cu. When the mass fraction of Cu exceeds 4%, al2cu and Al2CuMg are the main precipitates in the aluminum alloy matrix, and Cu poor areas are easy to appear near the precipitates. Due to the large potential difference between the Cu poor area and the precipitated interphase electrode, intergranular corrosion is very easy to occur. Therefore, 2024 aluminum alloy has poor corrosion resistance. At present, the most common treatment method in industrial production is to roll a layer of pure aluminum on the surface of 2024 aluminum alloy in the hot rolling treatment stage to improve corrosion resistance and anode protection. High purity aluminum is wrapped on the outer surface of the alloy. As aluminum is an active metal, the part in contact with air will form a layer of dense aluminum oxide film, thus providing good corrosion protection for the alloy. In addition, the aluminum clad layer has a higher potential than the 2A12 aluminum alloy matrix and plays an anodic protection role. Even if there are small cracks on the aluminum layer on the material surface, it can still protect the aluminum alloy matrix alloy.
As pure aluminum is relatively soft, 2024 is a hard aluminum alloy, and their physical and chemical properties are quite different. Rolling a layer of pure aluminum directly on the surface of 2024 aluminum alloy will lead to defects such as uneven aluminum coating and fracture of aluminum coating. Therefore, there are certain requirements for the aluminum coating process of 2024 aluminum alloy. In the 2024 aluminum alloy processing process, the aluminum coating treatment of the alloy plate is completed at the early stage of hot rolling. 1050 aluminum alloy is selected as the material for the aluminum clad layer of the plate (the composition is 0.2%~0.3% Fe mass fraction, 0.1%~0.3% Si mass fraction, and the sum of Fe and Si mass fractions shall not be greater than 0.45%). Before hot rolling, the contact surface between 2024 and 1050 aluminum alloys shall be cleaned. After removing the oil stain and aluminum powder on the surface, aluminum clad plates shall be placed on the upper and lower surfaces of the alloy ingot. In order to prevent edge cracking during rolling, two side aluminum clad plates shall be placed on the ingot before rolling; In the hot rolling process, the side is rolled, and the side of the plate blank is welded after several passes. The pure aluminum on the side fills the alloy cracks at the edge of the plate, increases the plasticity at the edge of the plate and strip, and reduces the edge cracks and strip breaks during medium temperature rolling and cold rolling.
The optimum solution treatment temperature for 2024 clad aluminum after rolling is 495 ℃. If the temperature is lower than this temperature, the alloy cannot be completely solution treated. If the temperature is too high, the performance will decline. The best solid solution time for 1.5 mm thick aluminum alloy clad plate is 35 min. the heat preservation time for solid solution treatment is too long. The Cu element on the side of 2024 aluminum alloy substrate will diffuse into the aluminum clad layer, resulting in serious pollution of the aluminum clad layer and the inability to form a uniform and dense aluminum oxide film on the surface, which reduces its protective effect on the aluminum alloy clad plate. At the same time, the diffusion of Cu element will reduce the potential difference between the aluminum clad layer and 2024 aluminum alloy substrate, Weaken the anodic protection of aluminum coating.
The maximum allowable deformation range of 2024 clad aluminum plate is 12%~16%. Excessive deformation will lead to large orange peel on the plate surface, and breakpoints or even jagged cracks on the aluminum clad layer, which will reduce the corrosion resistance of the material. 2024 aluminum alloy has good mechanical properties and corrosion resistance after aluminum coating process, annealing and solution heat treatment. It can be used as aircraft skin material to meet the development needs of aerospace technology.